SLA
SLA Design guide
Printing resolution
Standard layer thickness: 100 µm Accuracy: ±0.2% (with a lower limit of ±0.2 mm)
Size limitation 144 x 144 x 174 mm Minimum thickness Minimum wall thickness 0.8mm – With a 1:6 ratio
Etching and Embossing
Minimum height and width details Embossed: 0.5 mm
Engraved: 0.5 mm
Enclosed & interlocking volume
Enclosed parts? Not recommended Interlocking parts? Not recommended
Piece assembly Restriction
Assembly? No
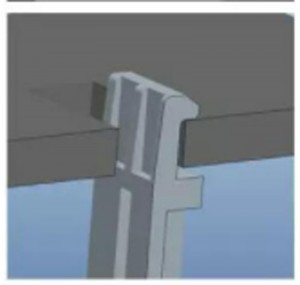
Engineering Expertise and Guidance
Engineering team will help you on optimize molding part design, GD&T check, material selection. 100% ensure the product with high production feasibility, quality, traceability
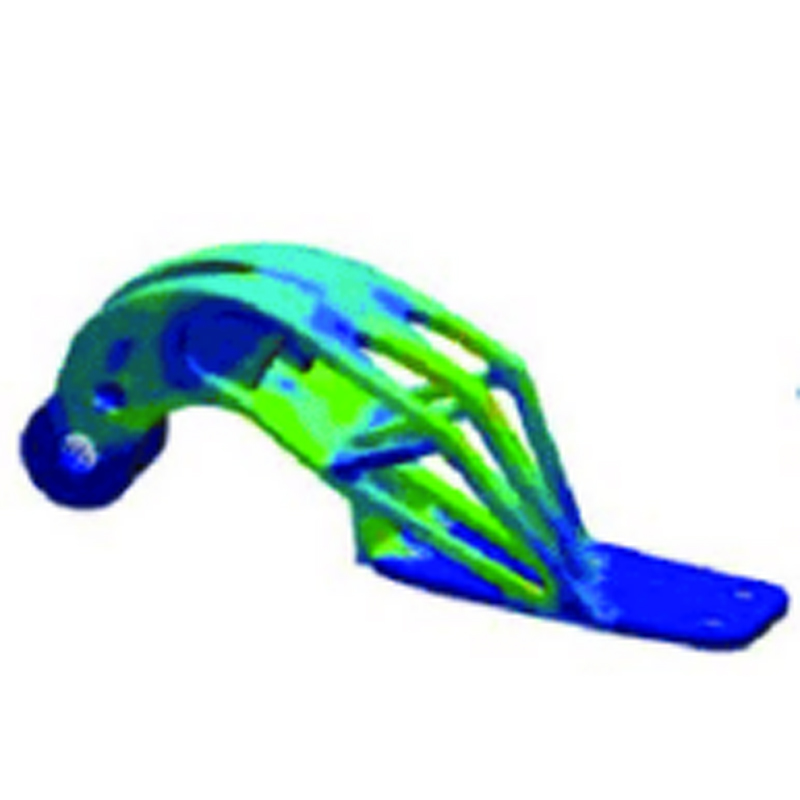
Simulation before Cutting Steel
For each projection, we will use mold-flow, Creo, Mastercam to simulate the injection molding process, machining process, drawing process to predict the issue before make physical samples
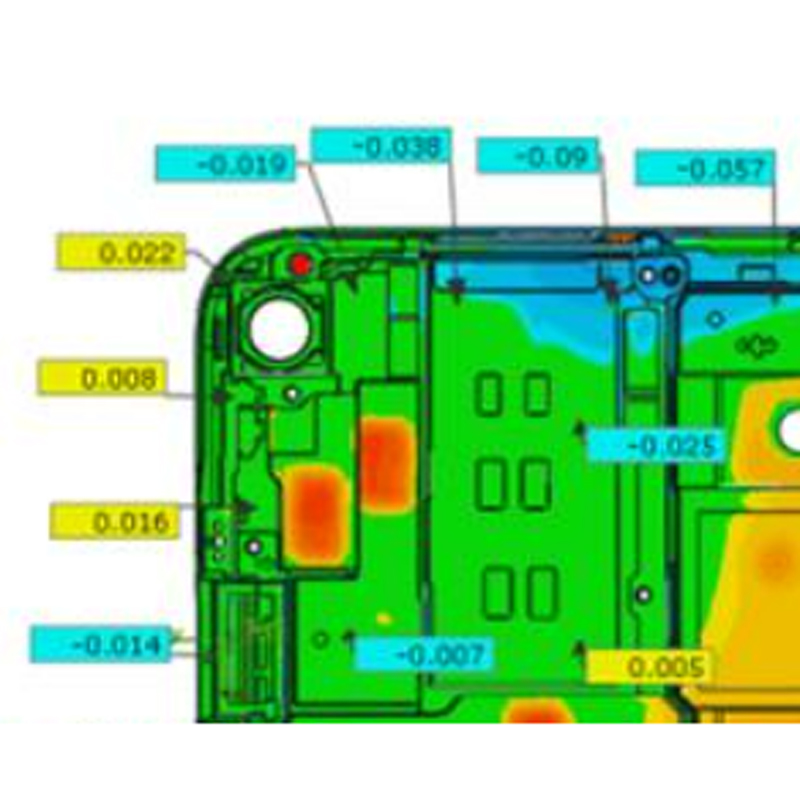
Complex Product Design
We have the top brand manufacturing facilities in injection molding, CNC machining and sheet metal fabrication. Which allows complex, high precision requirement product design
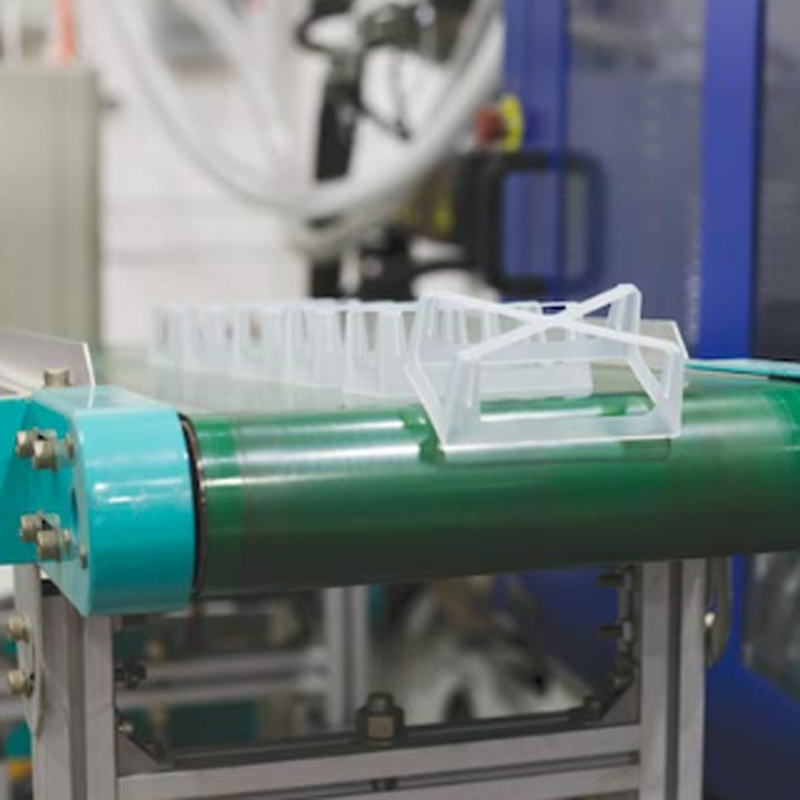
In house process
Injection mold making, Injection molding and second process of pad printing, heat staking, hot stamping, assembly are all in house, so you will have much low cost and reliable development lead time
Benefits of SLA Printing

High level of details
If you need accuracy, SLA is the additive manufacturing process you need to create highly detailed prototypes

Various applications
From automotive to consumer products, many companies are using Stereolithography for rapid prototyping

Design freedom
Design-driven manufacturing allows you to produce complex geometries
SLA Application
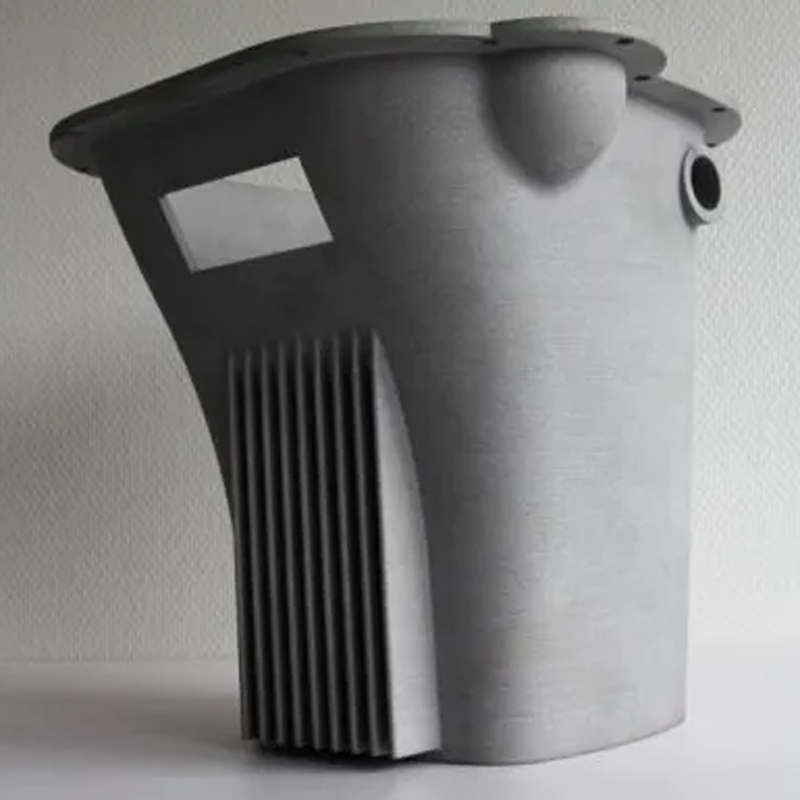
Automotive
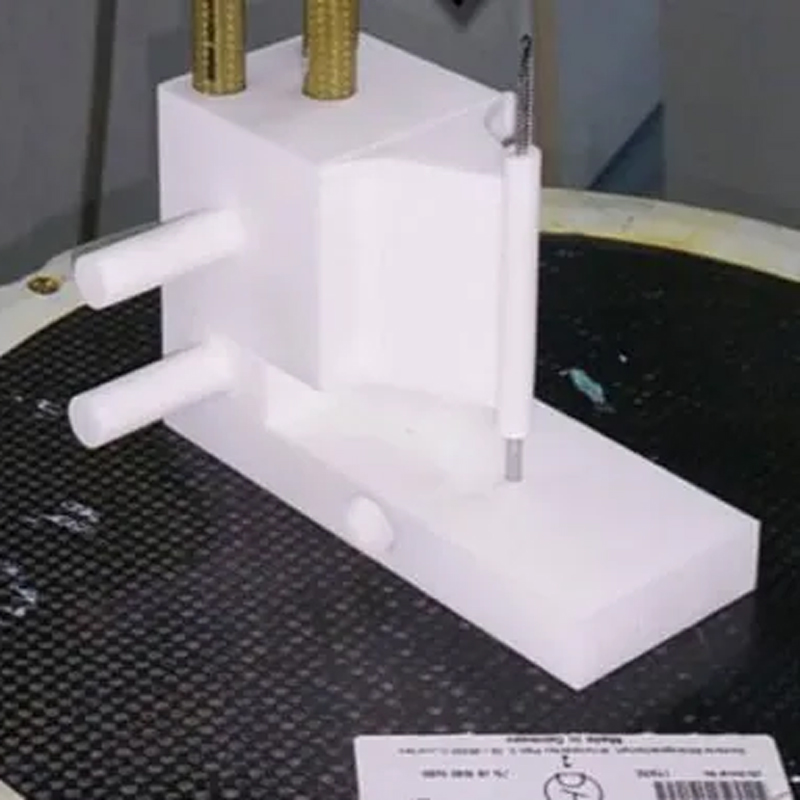
Healthcare and Medical
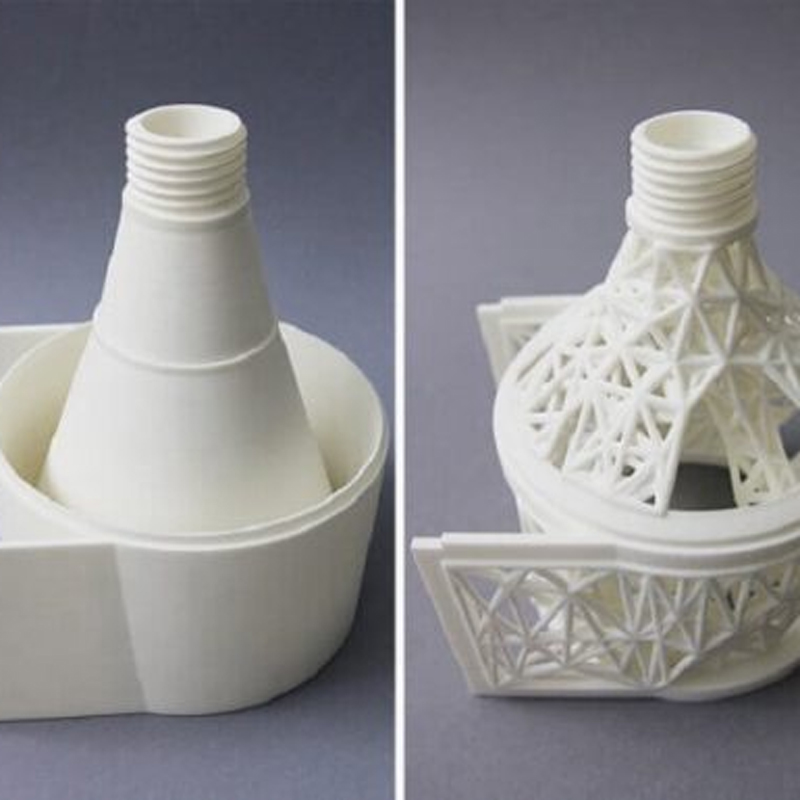
Mechanics
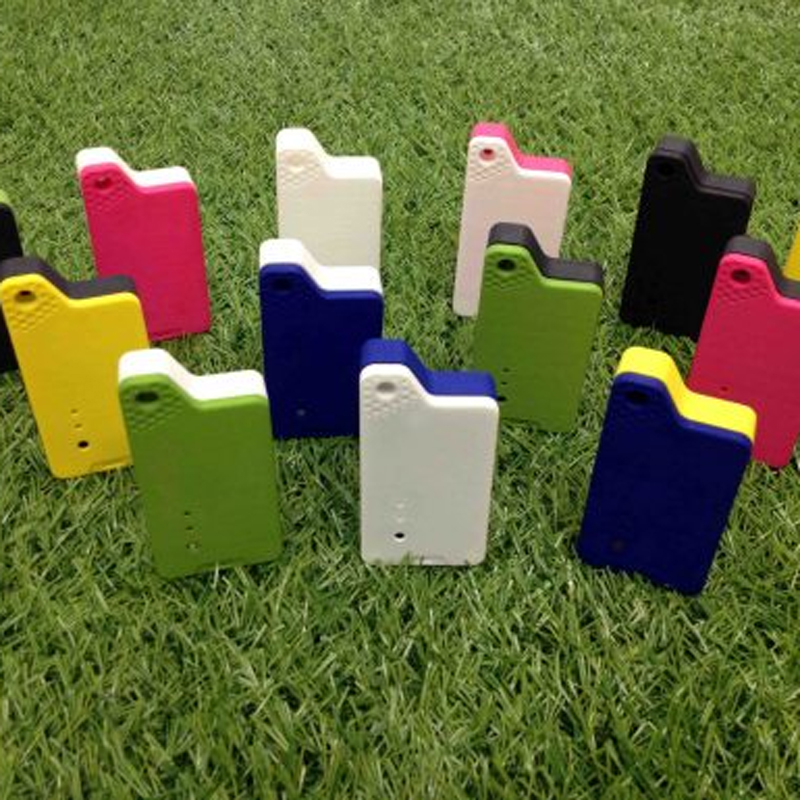
High Tech
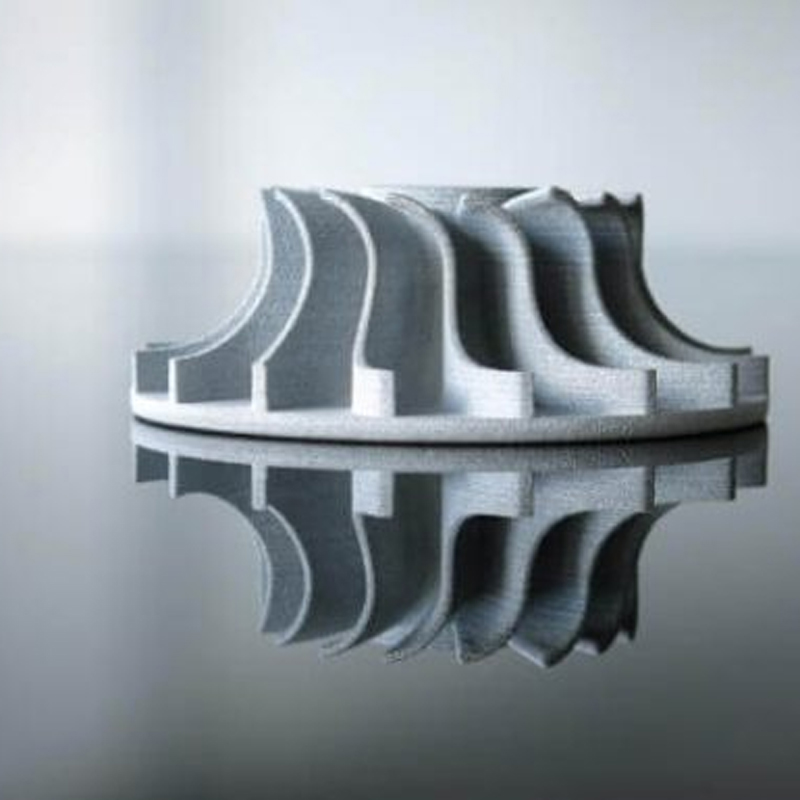
Industrial Goods
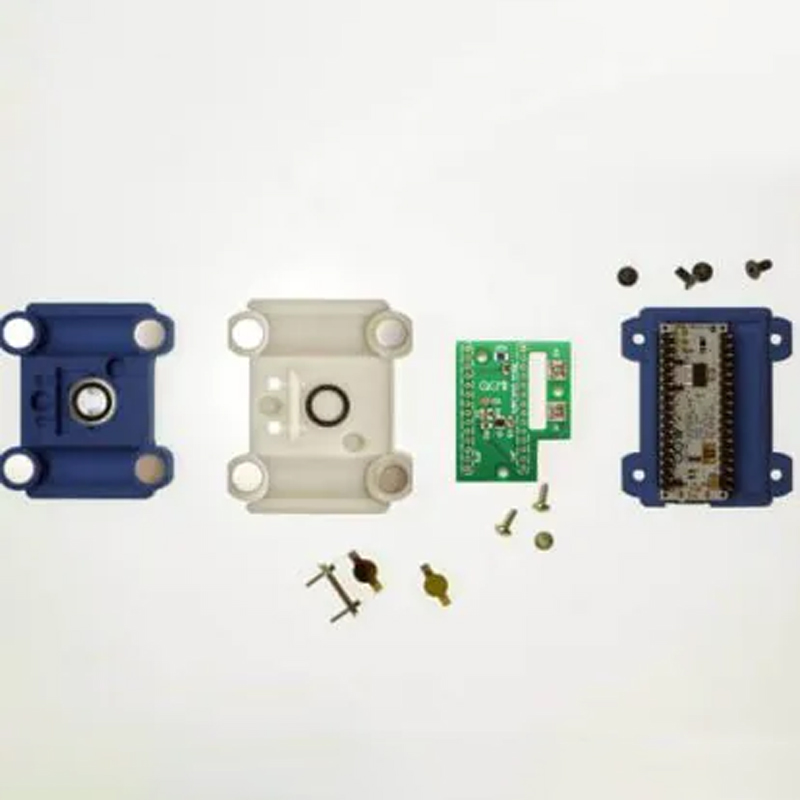
Electronics
SLA vs SLS vs FDM
Property Name | Stereolithography | Selective Laser Sintering | Fused Deposition Modeling |
Abbreviation | SLA | SLS | FDM |
Material type | Liquid (Photopolymer) | Powder (Polymer) | Solid (Filaments) |
Materials | Thermoplastics (Elastomers) | Thermoplastics such as Nylon, Polyamide, and Polystyrene; Elastomers; Composites | Thermoplastics such as ABS, Polycarbonate, and Polyphenylsulfone; Elastomers |
Max part size (in.) | 59.00 x 29.50 x 19.70 | 22.00 x 22.00 x 30.00 | 36.00 x 24.00 x 36.00 |
Min feature size (in.) | 0.004 | 0.005 | 0.005 |
Min layer thickness (in.) | 0.0010 | 0.0040 | 0.0050 |
Tolerance (in.) | ±0.0050 | ±0.0100 | ±0.0050 |
Surface finish | Smooth | Average | Rough |
Build speed | Average | Fast | Slow |
Applications | Form/fit testing, Functional testing, Rapid tooling patterns, Snap fits, Very detailed parts, Presentation models, High heat applications | Form/fit testing, Functional testing, Rapid tooling patterns, Less detailed parts, Parts with snap-fits & living hinges, High heat applications | Form/fit testing, Functional testing, Rapid tooling patterns, Small detailed parts, Presentation models, Patient and food applications, High heat applications |
SLA Advantage
Stereolithography Is Fast
Stereolithography Is Accurate
Stereolithography Works With Different Materials
Sustainability
Multi-Part Assemblies Are Possible
Texturing Is Possible